UHB Tape
FIANZA 12100C Technical Data
Technical Description
Unit Of Measurement
Technical Value
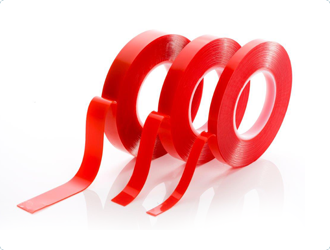
Unless stated otherwise all values given are average. All of the tapes in our range should be thoroughly tested on the substrates in the particular application they are intended for. The customer has to decide on the tapes suitability for the intended application.
Foamed Acrylic Tape 12110W Technical Data
Technical Description
Unit Of Measurement
Technical Value
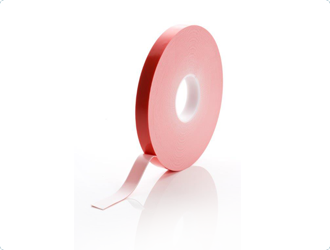
Unless stated otherwise all values given are average. All of the tapes in our range should be thoroughly tested on the substrates in the particular application they are intended for. The customer has to decide on the tapes suitability for the intended application.
UHB 9120G Foamed Acrylic Tape
Indasol UHB-9120G is a pure foamed acrylic bonding system. It is ideally suited to bonding difficult and dissimilar substrates and surfaces, including metals, glass, cermics, many plastics and even painted, lacquered or powder coated finishes such as stiffening bars on the reverse of sign systems and cabinets.
The foamed acrylic construction, provides excellent conformability and is therefore ideal for rough, uneven and structured surfaces. In addition the foam offers excellent sealing dampening and vibration absorbtion capabities, ensuring that bonded joints remain permantly secure, even in critical and exacting applications. Also, at this thickness, differing tensions and thermal expansions between the substrates are accommodated and absorbed by the acrylic foam mass.
Indasol UHB-9120G has good initial tack, combined with its superior bonding characteristics, enabling easy assembly and positioning. This product is therefore ideal for all permanent fixing and mounting applications of component parts and outdoor use. For demanding applications under high stress forces such as road traffic signage, or if bonding to difficult and low surface energy substrates, use Indasol UHB-9120G in conjunction with Indasol Surface Primer following the application instructions.
INDASOL 9120G is especially good on Low Surface nergy substrates and bonding onto cold surfaces
Technical Data
Technical Description
Unit Of Measurement
Technical Value
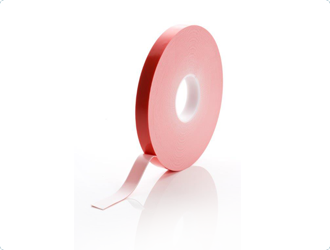
Unless stated otherwise all values given are average. All of the tapes in our range should be thoroughly tested on the substrates in the particular application they are intended for. The customer has to decide on the tapes suitability for the intended application.
High Performance Bonding, Sealing & Preparation Products
Over View & Usage
Acrylic technology has been around for over 20 years and was originally developed for use in applications where an Ultra High Bond (UHB) was required. These applications varied from MOD Marine, Aerospace, Automotive and General Manufacturing. Once established as a viable long term bonding solution, UHB products have been used in many different types of Industrial bonding applications as successful replacements to methods such as rivets, welds, screws, sealant adhesives and other messy time consuming adhesive products.
UHB pure foamed acrylic bonding system is ideally suited to bonding difficult and substrates and surfaces, including metals, glass, cermics, many plastics and even painted, lacquered or powder coated finishes such as stiffening bars on the reverse of sign systems and cabinets where a strong long term bond is required. The foamed acrylic construction, provides excellent conformability and is therefore ideal for rough, uneven and structured surfaces. In addition the foam offers excellent sealing dampening and vibration absorbtion capabities, ensuring that bonded joints remain permantly secure, even in critical and exacting applications. Also, at this thickness, differing tensions and thermal expansions between the substrates are accommodated and absorbed by the acrylic foam mass. Some of the products will even allow movement of parts under stoving cycles above 250°C.
Within the range we have High Temperature products, Cold Stick products, Flame Retardant products and Automotive Approved products. Available in a range of thicknesses, widths and colours, our UHB products offer an all round clean and efficient bonding solution for most applications. It is advised with all UHB materials that the application guide is followed in all applications.
UHB tapes are visco-elastic by nature their strength and rigidity is a function of the rate at which they are stressed. This means that they tend to react stronger and with more resistance under relatively faster rates of stress load (dynamic stress forces) and tend to demonstrate greater creep tendencies with static loads over longer periods of time. As a general rule, and we cannot be specific for every substrate , a 6,000sqmm area of tape (eg80mm x 75mm), when applied correctly and allowed to attain ultimate bond strength, should be used to support each Kg of weight without excessive creep.
Under shorter term static shear and dynamic shear forces, we have demonstrated that a 625sqmm area of tape (eg 25mm x 25mm), properly applied and at ultimate bond strength, will hold a 1 Kg weight. Because of the points afore mentioned, however regarding long term static loads and their effect on creep, we would always suggest building in safety margins to accommodate and allow for any detrimental movement over time. It is important to recognise the forces that will be acting upon the tape in service. For shear applications, always try, wherever possible, to apply the tape in the ‘shear direction’ ie. The strips should be applied with the length vertically so as to resist the shear force or tendency to creep. The values presented in this document have been determined by standard test methods and are average values that should not be used for specification purposes. Our recommendations regarding the use of our products are based on tests considered by Industrial Adhesive Solutions to be reliable, but the customer must conduct his own tests to determine the suitability of the product to the individual application and requirement . Industrial Adhesive Solutions do not accept responsibility or liability directly or consequentially , for loss or damage caused as a result of our recommendations. Use appropriate cleaning and priming products where advised such as IPA, SP-450 and PR-100 .
Application Guide for using UHB Tapes
As with all Tape products, please ensure the surfaces to be bonded are Clean, Dry and Dust Free
In some cases it may be advisable to abrade the surface slightly using a nylon abrasive pad.
Surfaces should be either cleaned with IPA then primed, or cleaned and primed in one.
Cleaning – This is available as either a liquid, pre impregnated sachets or pre impregnated wipes. These are only a surface cleaner.
Priming – Primer can also be used where IPA has been used to clean initially. This is an optional process, however this does improve initial grab and bond performance.
Cleaning and Priming in one – For all of the above – Apply to a lint free cloth and wipe the first surface in one direction. Apply a second amount to a fresh face of the cloth and repeat. Do this again on the second surface.
Once the Surface has dried (15-20 sec), apply the UHB Tape to one surface. Use a rubber roller to apply an initial downward pressure to ensure the UHB is well bondedto the first Surface.
Large surface areas where either a high amount of weight or tension may be present vertical and horizontal strips of UHB should be used to increase bond strength
Remove the backing liner and bond the second substrate. As this type of tape responds to pressure, ensure as much pressure as possible is applied to give the best bond.Use a roller where possible.
Handling strength will be gained immediately and full strength will be gained over a period of 24 to 72 hours
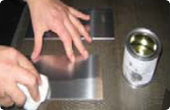
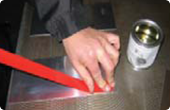
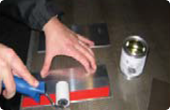
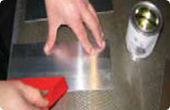
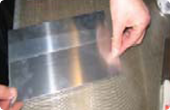